Volution Bearing Fundamentals Explained
The Ultimate Guide To Volution Bearing
Table of ContentsThe 9-Second Trick For Volution BearingThe Facts About Volution Bearing UncoveredThe Facts About Volution Bearing UncoveredVolution Bearing for Beginners
This is the amount of time that a team of obviously identical bearings will certainly finish or surpass before the development of a fatigue spall. The standard formula for determining bearing L10 ranking life is: where: C = Dynamic Capability (dN or Pounds) P = Equivalent Bearing Lots (N or Lbs) N = Rotating rate in RPM e = 3.0 for sphere bearings, 10/3 for roller bearings All ball bearings, tapered roller bearings, and round roller bearings are qualified of taking a substantial axial thrust load.This calculation can be somewhat made complex as it relies on the family member magnitudes of the radial and drive tons to each other and the contact angle developed by the bearing. It would certainly be too tough to reveal all the approaches of computing P for all the bearing types shown. For conical roller bearings, the "K" drive factor is utilized.
Radial round roller bearings that have opposing flanges on their inner and outer races have a restricted capacity of taking a drive load though the length of the rollers. It is so minimal that we do not recommend individuals purposefully do this. Acceptable thrust loading is utilizing roller ends and flanges for intermittent thrust and finding objectives.
Numerous applications do not run at a consistent load or speed, and to pick bearings for a specific ranking life in hours based on the most awful operating condition might verify uneconomical (http://go.bubbl.us/e1e5c0/dad4?/Volution-Bearing). Typically, a duty cycle can be specified for the numerous operating problems (tons and rate) and the portion of time at each
Indicators on Volution Bearing You Need To Know
In such instances, a complete duty cycle happens within one change of the bearing. The 2 examples might be incorporated for several awaited operating problems with reciprocating movement and different optimal tons and speeds. Determining the rating life when tons and rates vary entails first computing the L10 rating life at each operating condition of the responsibility cycle.
T1, T2, Tn = percent of time at different problems, shared as a decimal T1 + T2 + Tn = 1 Lp1, Lp2, Lpn = Life in hours for each period of constant lots and speed When a bearing does not make a complete turning yet oscillates back and forth in operation, a lower comparable radial load can be calculated using the formula below: Pe = Po x (/ 90)1/e where: Pe = equal vibrant radial load Po = actual oscillating radial tons = angle of oscillation, in levels e = 10/3 (Roller Bearings) 3.0(Round Brgs) Some applications produce really high radial and drive loads, and it might not be physically possible or viable to utilize a single bearing that can taking both sorts of lots.
When this takes place, the device developer must beware to ensure that the radial bearing takes only the radial load, and the drive bearing takes just the drive lots. A great method to complete this is to use a cylindrical roller bearing with one straight race at the "radial" location, as this bearing can not take any kind of drive.
One means to achieve this is to make the fit of the outer races really loose in their housings: typically.5 mm/.020 In. to 1.0 mm/.040 In. Life adjustment variables allow the original devices producer to better anticipate the actual solution lives and dependability of bearings that you select and set up in your equipment.
Getting The Volution Bearing To Work
Life modification factors, a1, a2 and a3, can theoretically be higher or less than 1. manufacturer.0, depending upon their analysis. In the OEM's process of anticipating the solution reliability of his/her equipment, it is sometimes necessary to enhance the integrity of the selected bearings to anticipate a much longer suggest time between failings
If a reduced worth for L10 is calculated with an a1 aspect, and it is not appropriate, then a bearing with higher Dynamic Capability needs to be chosen. Dependability - % Ln a1 aspect 90 L10 1.00 95 L5 0.64 96L4 0.55 97 L6 0.47 98 L2 0.37 99 L1 0.25 There have been several enhancements in birthing layout and manufacture over the years that have actually been shown in life tests that cause improved L10 ranking life.
Many bearing applications are much from research laboratory conditions. It can be challenging to justify an a3 element greater than 1.0. Problems such as high temperature level, contamination, outside vibration, etc will result in an a3 element much less than 1. If the lubrication is exceptional and the running rate high sufficient, a considerably enhanced lube movie can establish in between the bearing's inner contact surfaces validating an a3 factor more than 1.0.
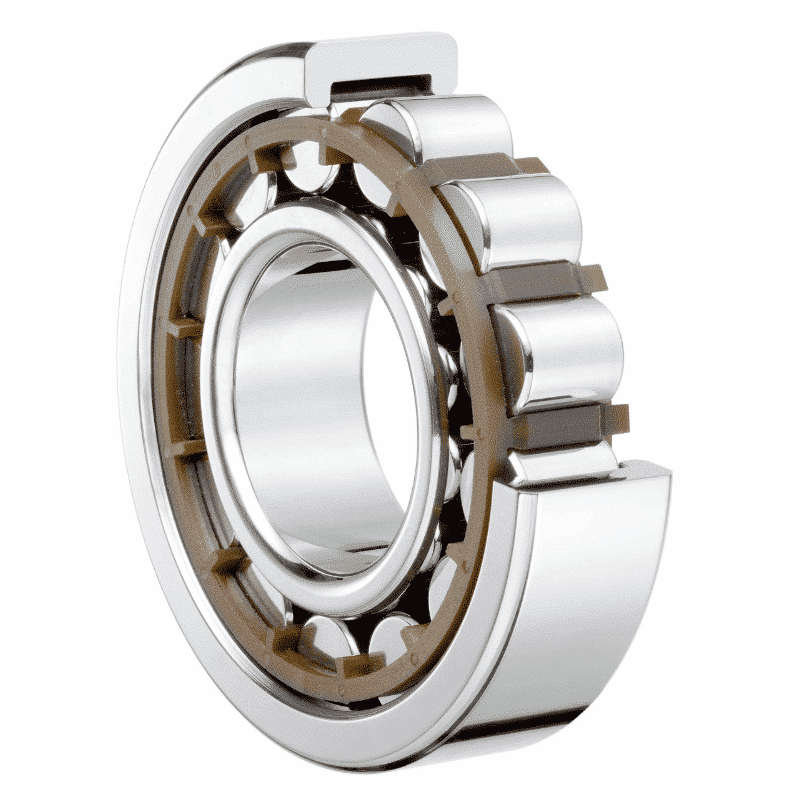
Some Of Volution Bearing
The complying with formula is used to compute the System Ranking Life: L10sys = (L1-w + L2-w + Ln-w)-1/ w this post where L10sys = score life for the system of bearings L1, L2, Ln = score life for the private bearings in the system w = 10/9 for sphere bearings and w = 9/8 for roller bearings It has actually been learned from experience that bearings need a minimal applied lots to guarantee grip for the moving aspects so they roll as the shaft begins to revolve. https://anotepad.com/note/read/6j5dsg3a.
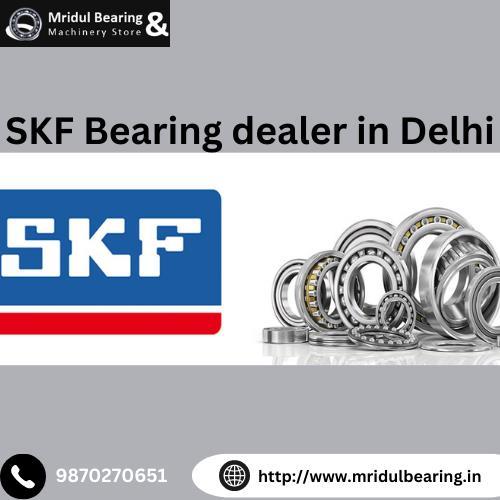